Kontaktirajte nas
Telefon
Аустрија
22.02.2022
Assembly system replaces manual setting of blind rivet nuts
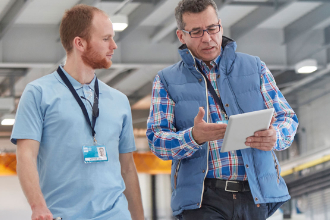
In focus - process optimization and quality improvements as well as time and cost savings
It started with an "Expert Walk" and ends with a semi-automated station for the fast and, above all, safe, precise setting of blind rivet nuts.
What the customer particularly appreciated: Our experts not only made their know-how and experience in fastening and assembly technology available, but also supervised the transition "from manual to automatic" from the in-depth situation analysis of production to individual modifications the riveting station.
But first things first: A company that, as the world market leader and manufacturer of compact systems, is continuously expanding its market share in its industry, has the blind rivet nuts processed "by hand" during production, which means: With currently around 200 components per day, the employees* have to insert the blind rivet nuts one by one with a manual setting tool – this amounts to almost a quarter of a million parts per year, and the trend is rising.
Build on the consulting expertise of the Bossard / KVT experts from start to finish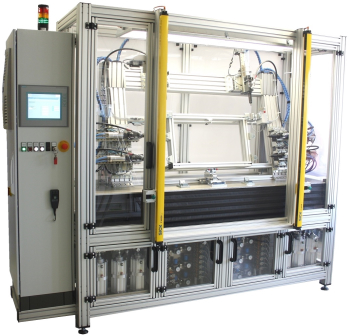
Even if there was certainly nothing against the economic benefit, it was actually the aspects of "process optimization and the associated quality improvements that were in the foreground for our customer," says Andreas Reiger, technical (sales) consultant.
Together with Business Development Manager Stefan Landthaler, he acted as a permanent contact for all questions relating to the riveting station, including its customer-specific adjustments.
They were supported by Horst Sälzle, Head of Engineering & Services, who and his team are promoting the areas of "Assembly Technology Expert" and "Smart Factory Logistics" in Illerrieden.
System Sells. Time savings, higher quality, cost reduction, fasteners and processing technology from a single source as well as comprehensive engineering and services, also on site. The strict focus on added value for the customer also led to success and cooperation here.
As a machine partner to solve the requirements, Landthaler and Sälzle resorted to a proven company that had the right machine in its portfolio, which had to be adapted in detail to the specific framework conditions and wishes of the customer.
Important criteria for the riveting station included space requirements, user interface, technical availability, maintenance and repairs, energy assessment, compliance with all standards and regulations, and last but not least, ergonomics for working with as little stress as possible. Stefan Landthaler fine-tuned and optimized the detailed application/functionality of the riveting station in constant exchange with the customer.
Process quality in focus
The production process: The setting process of the blind rivet nuts is triggered automatically, which means: the nuts are automatically fed, threaded onto the threaded mandrel, positioned and set in the sheet metal. Stefan Landthaler: "The straight seat of the blind rivet nut and a firm seat are basic requirements for perfect process quality, which is guaranteed by the riveting station including monitoring."
Other arguments with which the riveting station used scores points: It can be easily and conveniently relocated, and changing the wearing part "inserting mandrel" or converting to a different blind rivet nut is a matter of a few simple steps, without the device having to be readjusted afterwards becomes necessary.
Subscribe to KVT Newsletter now and stay updated with our latest product and service highlights!